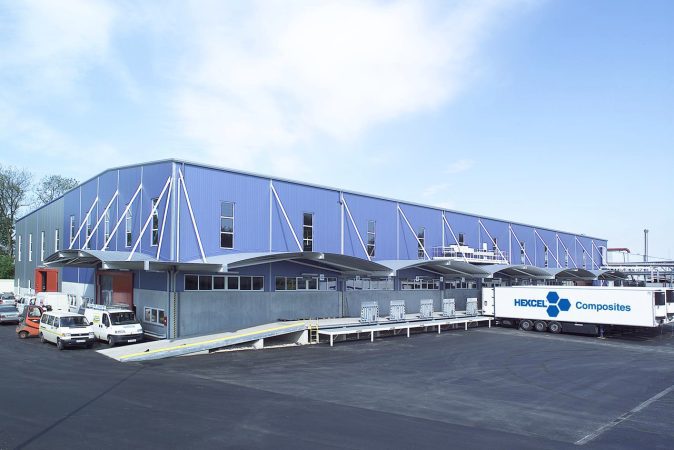
Hexcel Launches environmentally Friendly Nature Range
Hexcel a global leader in advanced composites had long been a major supplier to the wintersports market and has recently launched its environmentally friendly new Nature range. Source met up with Hexcel to hear all about its latest green initiatives.
Firstly, can you give us a short introduction to tell us how Hexcel supports the winter sports industry?
Since the early 1970’s, when it manufactured the first composite skis at industrial scale, Hexcel has been a trusted partner to the winter sports industry. Hexcel supplies a comprehensive portfolio of products, including HexPly® prepregs, Polyspeed® laminates, and Modipur® polyurethanes, to industry leaders such as Elan, Head, Fischer, Kästle, Stöckli, Tecnica Group (Blizzard and Nordica), and Völkl.
Where does Hexcel manufacture materials for the winter sports industry?
Hexcel makes the bulk of its winter sports materials at Neumarkt, Austria. This central European location is perfect for rapid and responsive feedback on material testing and development with manufacturers. Hexcel and its predecessors have produced high-quality composites at Neumarkt since 1947, with the latest technology shift being the successful transition of its winter sports product range to the new HexPly® Nature bio-derived prepreg. This move includes the full conversion of HexPly® M78.1-LT prepregs to the more sustainable HexPly® Nature version, reflecting the company’s ongoing commitment to reducing the environmental impact of key materials for the ski and board sector.
How are Hexcel customers challenging your innovation teams the most?
Hexcel materials add value to composite structures by delivering performance or processing gains. We have a long history in winter sports and the prepregs we supply deliver a constant fibre-volume ratio, high stiffness, excellent fatigue properties and short cure cycles. Now, with the Nature range, we’re doing that in a way that reduces emissions and improves the overall sustainability of their products. Our customers were clear that the long term test performance of the multi-material adhesion was a critical factor as well as the “feel” of the ski on the snow itself.
How easily can the Hexcel Nature range be implemented by ski and snowboard manufacturers?
We’ve done a huge amount of work on this, benchmarking performance and independently validating how the materials perform and improvements we have made over the traditional HexPly systems. We have decades of experience for the standard systems and have been working on the Nature versions since 2021. Now we need to clearly communicate the options to ski and snowboard builders, helping them plan their own environmental strategies based on the trusted data we provide. Hexcel has commissioned its own LCA that clarifies the improvements made for the HexPly M78.1-LT prepregs. Natural fibres have also formed a large part of the development too, with the Hexcel team working to minimise the moisture content of the reinforcements before processing to maximise the mechanical performance.
What is the feedback from the manufacturers?
We have great feedback on the new Nature range products particularly on making the switch simple and the additional data we’re providing for environmental studies. Alberto Zanatta, Chairman, Tecnica Group, said “At Tecnica Group, we pride ourselves on delivering high-performance skis that meet the rigorous demands of our customers and the environment. Partnering with Hexcel to incorporate its Nature range of bio-derived prepregs into our series production process has been seamless. Hexcel’s advanced composite technology and commitment to sustainability have enabled us to transition smoothly without compromising the performance or consistency of our skis in series production and out on the mountain.”
Recycling and reuse of materials is a key factor in terms of raw materials. How does Hexcel provide options for ski and snowboard builders in this area?
This is a critical issue for Hexcel and the wider thermoset composite industry. The resins we create allow manufacturers to build incredibly light advanced composite structures. The chemistry we use forms exceptionally durable products that offer end-users a long lifetime of performance skiing and snowboarding with no loss of durability. Whilst the industry continues to develop raw materials and recycling processes that can help to recycle the composite materials used in winter sports equipment, Hexcel is also focused on parallel improvements that can help establish the groundwork for recycling winter sports hard goods and achieve a closed-loop system. Hexcel is a member of the FFG funded WINTRUST (Wintersport Resource Efficiency and Improved Circular Economy) project which will see skis and other equipment collected at centres in Austria before disassembly before being passed to processing experts who will evaluate the recycling options. Together with its industrial and research partners, Hexcel will help close the recycling loop for winter sports equipment.
www.hexcel.com