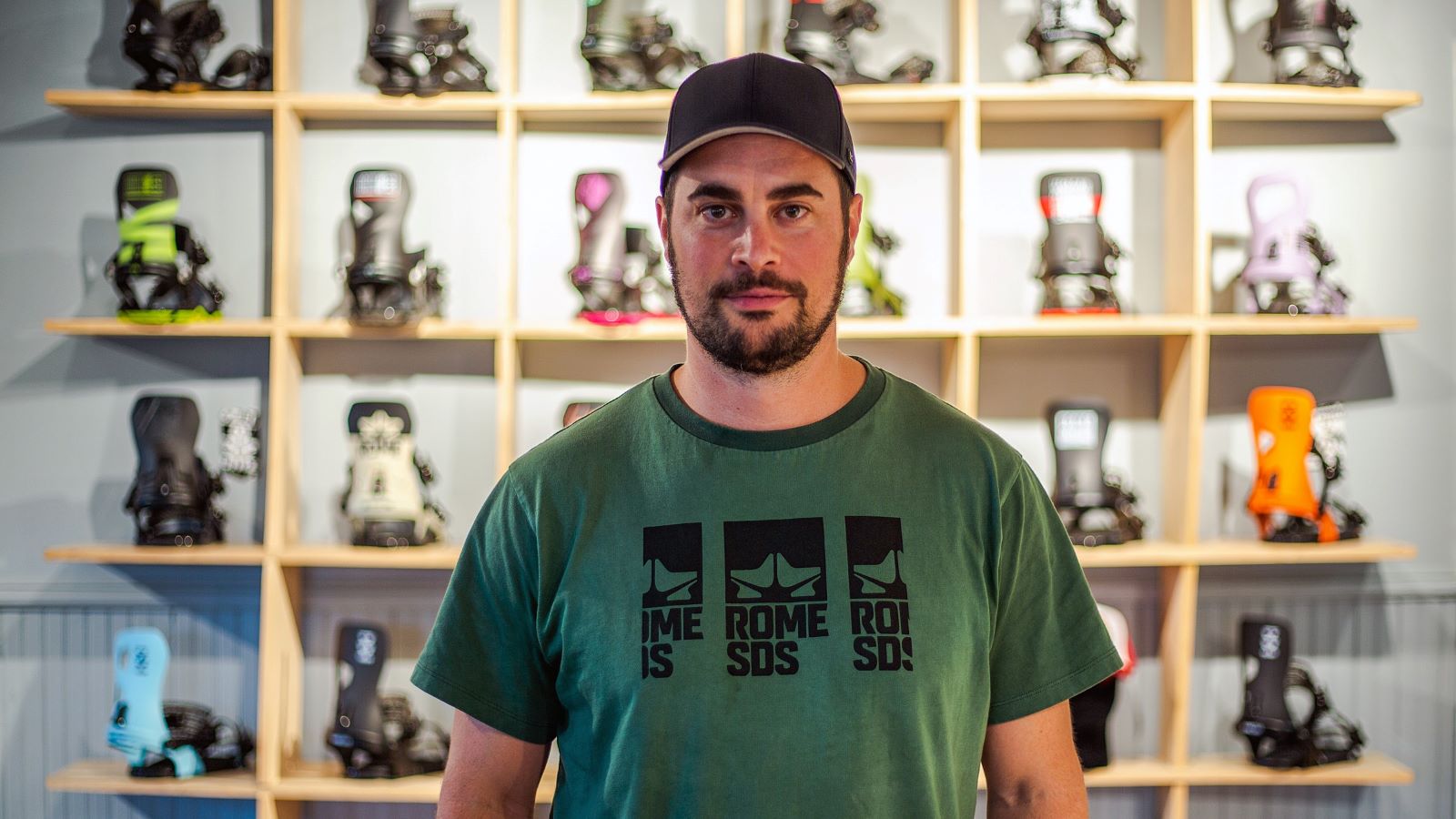
Justin Frappier: Rome’s Go-To Man for All Things Boots & Bindings
It’s been 10 years since Justin Frappier – Frap – joined Rome SDS; firstly, as their Senior Industrial Designer & Product Manager, before moving onto becoming their Director of Product Design & Development at the start of 2019. He has gained a great rep for designing boots and bindings, so we decided to learn some more about Frap, his career and what’s going on at Rome.
Justin, please could we have a plotted history of your career so far?
Sure! It’s been a wild ride! Skipping through the high school era (even though the art, hockey and snowboarding classes is where all the passion started). I ended up applying and getting into the School of Industrial Design at Carleton University in Ottawa, Canada.
Between school years, I landed some co-op/internship experiences at two design firms: DW Product Development in Ottawa, Canada, and then NPK Design in Leiden, The Netherlands. I’m super appreciative of Carleton’s program as well as the two cooperative work experiences at DW and NPK where I was able to learn and pick up in-depth skills, process knowledge, and know-how from two great design teams.
Right before graduation, I landed a job at Reebok/CCM Hockey on their product team and worked specifically in the protective category designing gloves. Eventually, I was asked to join the skate team and while it bothered me to be moved from one category to another, looking back, it resulted in my success at CCM and ultimately the reason for landing the gig at Rome. Working on skates was amazing because it blended many different types of materials and processes into one product. During the time I spent there, I was learning a lot – different materials, manufacturing processes, working with the suppliers overseas for the first time… it exposed me to many parts of the product creation process. On the business side of things, it also taught me that margins can be just as important as the product itself. It was with CCM that I was able to experience my first trips to Asia: China, Taiwan, and Thailand. I was bright-eyed at the time and being only 24 years old, going to Asia seemed unreal!
In early 2012, I was catching up with an old friend from Carleton who had moved from Montreal to work at Rome SDS. Long story short, it was he who convinced me to come down, meet the crew at the office and maybe go shred if there was time. There was no time to ride but I ended up landing the gig as Boot PM/Designer/Developer and started in March 2012.
A year or so in I was asked to help on bindings as well. At the time, the team was working on the original Katana so while I was not involved from the start, it was a great project to be a part of and help bring to market; mainly because the OG Katana set the stage for many more binding innovations in the years to follow.
It’s been an incredible journey at Rome – for so many reasons. First, we are a small team – currently 8 people in the Vermont office – which is where all the product creation happens. To think of the sheer volume of SKU’s we put out every year it’s quite an accomplishment and an amazing team to be a part of. Having been to many tradeshows, on-snow events and sales meetings over the years, the standout events that I’ll never forget are The Rome Lodge experiences in Austria and Italy. I’ve now been to China more times than I can count… must be at least 40 by now, and while I’m far from that bright-eyed 24-year-old I once was, I’m still learning new things about design and myself. Every trip over there results in both a better product and personal growth.
What have been the biggest lessons learned in the boots & bindings game in the past 18 months?
The supply chain is a mess. Material and shipping costs going up, lead times are longer because of the backlog at ports and staff shortages… all industries have faced a list of challenges since the start of 2020 and we need to adjust the process and timelines to stay ahead of it. On the design side, we are continuously looking at designing smarter assemblies (shared/modular parts, colours, or processes) to maximise the efficiencies at the factory or to speed up our design/development time so we can bring a dialled product to market to balance out some of the supply chain issues and cost hikes. This is also allowing us to focus our efforts on manageable project lists enabling us to simplify parts and dial them to perfection.
How’s the 22/23 collection looking? What are the biggest new developments?
The collection is looking dialled. We took the ‘incremental improvements approach’ this year to keep ourselves focused on development. We have new buckles – we ran magnifying glasses over our existing buckles and made some changes to improve the durability and reliability of both the buckles and the ladder straps. We have also integrated a new ‘Fast Entry’ technology into our ladders to improve the experience for our customers on snow. These ladders are designed to pop open naturally bringing your ankle and toe straps out of the way so you can step in and out of your bindings more easily, without stepping on your straps. And then we’ve got our newish AuxTech strap technology which are a big part of our connected-comfort story – I may be biased but these straps are the most connected and comfortable in the game.
How has working with the Low Pressure Studio/Nidecker Group helped development?
Specifically talking about binding product development, we’ve been able to collaborate and bring concepts through to production in a more timely and efficient manner. We’ve streamlined the process and assemblies to facilitate the sharing of components between both Rome and Bataleon brands, while still allowing both to maintain their own identities. Working with designers and engineers across the groups is always a rewarding experience because we are learning, inspiring, and pushing each other to bring better products to market – whilst still maintaining some friendly competition vibes. I also really appreciated being the lead in the Bataleon binding launch as it was an opportunity to approach design with a different aesthetic, and since Bataleon and Rome are produced at the same factory, it was an opportunity to improve binding quality for both. LPS and Nidecker are investing across all brands: we’ve hired employees in Seattle, Amsterdam, Rolle, and Vermont with further team expansions on the horizon. R&D investments have made a significant impact on bindings, and now that we have a state-of-the-art SLS printer in Vermont we can ride and test parts printed parts ourselves, which saves a ton of development time and tooling modification costs.
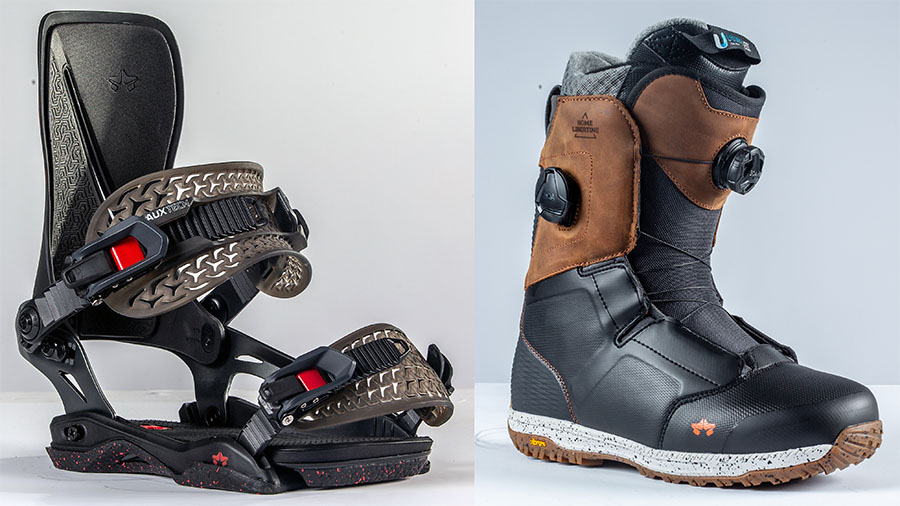
Katana & Libertine x BOA
Which of the materials that you use has been the most affected by Covid?
In bindings and boots, it is hard to say because it is always changing depending on the month, week, or day; some vendors in different parts of China had slowdowns because of Covid outbreaks and things would shut down intermittently without warning. These days we just plan to assume everything will have a longer lead time and so we are constantly pushing up development timelines, order deadlines, production schedules, etc…, so we can reduce the chance of late products hitting the shelves. It has been a huge challenge for all industries and the hope is that things will settle down soon.
How were deliveries globally for you this winter?
Mixed bag. Some stuff arrived early but sat somewhere; in a port, a shipping yard, or an unknown location(s) with limited updates or communications on when it would arrive. Here’s to hoping the worst is behind us!
What’s Rome’s point of difference in bindings?
For Rome we pride ourselves on technologies that offer connected-comfort, customisation, and responsiveness. Without a doubt, we pride ourselves in saying that Rome bindings are the most customisable bindings on the market. We often use the car seat analogy – everyone has a different body type and their own preference when it comes to driving style and comfort. Adjusting your binding is the same and our customisation features allow you to size adjust as well as performance adjust. A perfect example of this performance adjustment is the PivotMount Max which allows you to adjust your bindings’ response, power, and tweakability with one component.
Our Underwrap technology makes Rome bindings extremely responsive. The aluminium Fullwrap and Asymwrap heelcups allow the binding to stay lightweight without sacrificing power. Asym has a bit more surf side-to-side while Full has more power. These underwrap chassis are a hybrid construction; a forged aluminium heelcup wraps from heel to toe and under the baseplate so we can keep our bindings lightweight and responsive.
In your mind what were the two most important game-changer Rome models in both boots and bindings during the last 15 years and why?
The OG Katana with the industry-first Asymwrap chassis was the game-changer for us. It was the new benchmark of what Rome bindings could be. Before that, we had very good bindings, but the main drawback was they were overly complex with different parts for each model: they were bulky and heavy compared to other brands. Since that OG Katana, we have slowly plugged away and applied a lot of design thinking to our entire binding line. All models are now lightweight without sacrificing the performance and customisation Rome bindings are known for.
In boots, I would say it’s not a specific model but the 3rd party material collaborations we have in our boot line – BOA fit systems for a dialled-in fit, the space-aged Ultralon foam in our liners, and Vibram outsoles for max grip. These material technology collaborations have helped our boot line to grow year after year.