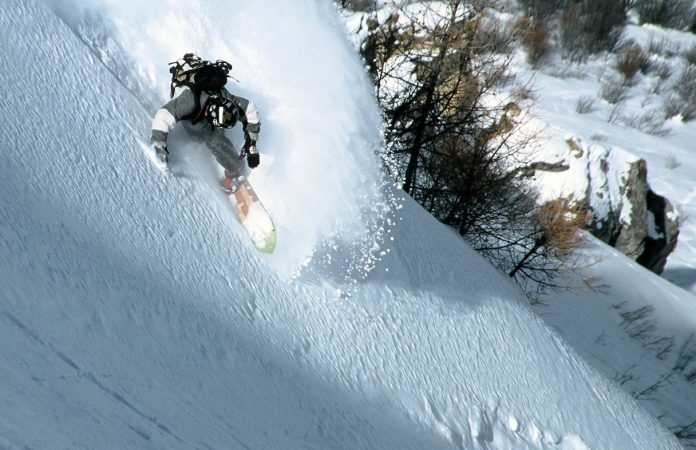
Sicomin Leading The Way In Sustainable Resins
Sicomin a leader in the development of epoxy resin systems has been developing products that offer longterm sustainable solutions to the Winter Sports industry. Source sat down with Sicomin to hear how these low impact epoxies are being taken up by brands and integrated into their products.
Can you give us a quick introduction on how Sicomin supports the ski and snowboard manufacturers?
Sicomin has supplied the Winter Sports sectors for over 40 years. This includes the development of sustainable bio-based epoxies, with its market-leading GreenPoxy range offering manufacturers a lower impact solution. Both high-volume and smaller custom ski and snowboard brands have used Sicomin’s traditional epoxy systems for many years. Now, the majority have switched to GreenPoxy with volume-based manufacturers typically using the GreenPoxy 33 and 28 systems and bespoke builders using GreenPoxy 56 for hand made skis and boards.
Is it a challenge to get the ski and snowboard builders to accept the integration of lower impact materials?
Initially it was a challenge to develop more sustainable resin systems that maximise plant-based bio-content whilst also delivering uncompromised mechanical performance. Once we’d created the products, and demonstrated how well they work, we found that ski brands and their customers are just as keen as we are to reduce environmental impact.
There was always the concern that bio-based materials were a premium product or that supply could be an issue. Therefore, Sicomin has invested massively in GreenPoxy production, making sure these materials are available in industrial volumes and that we can provide a low-risk, stable supply chain for builders working with large scale series production.
How are winter sports OEMs developing their products to include more sustainable materials?
We have great connections with the technical teams that handle materials testing and evaluation. Our European factories in France mean we can easily supply existing or newly developed products just when they need them. This is what happened with GreenPoxy 28 and the Salomon HIGHPATH boards. Aiming to set a new benchmark for eco snowboard production, Salomon selected a package of bio-based and recycled materials including: GreenPoxy 28 resin with 28% of its carbon content derived from plant sources; an FSC certified core; bamboo veneers; a castor bean topsheet, as well as 50% recycled content in the base and 20% recycled aluminium in the edges.
The use of bio-based resins, along with a complete review of the other materials in the board, underscores Salomon’s dedication to creating products that deliver exceptional performance while minimizing ecological impact. GreenPoxy resins are not just used in the HIGHPATH, they are also in the Assasin, Assasin Pro, Huck Knife, Huck Knife Pro, Rumble Fish, Super 8, Dancehaul Pro and other Salomon boards.
Does Sicomin also offer technical support to smaller brands?
Absolutely. Our position in France keeps us very close to the European ski and snowboard teams. We’ve also got our global distribution base that handles shipments to North America, Asia and North Africa where our other board building customers are based.
We’ve recently started to support MADskis in Switzerland. MAD was formed by freeride champion Aurélien Ducroz and mountain guide Eric Gachet, and we also supplied the resins for Aurélien’s world championship winning flax and glass fibre Class40 yacht. MAD creates incredible “natural look” skis using natural fibers bonded with GreenPoxy bio-sourced resins and wooden top sheets.
We have also been supporting Jérôme Parent at Swiss custom ski brand LIMPID. Jérôme first shaped skis in 2007 before launching LIMPID in 2019, with Sicomin resins providing the flexibility to produce a fully customizable ski portfolio using locally sourced materials. Finally, we also work with Phenix Snowboards, specialists in swallowtail, freeride and split boards for the touring and alpine riders. In all cases, smaller builders – who have much more direct contact with our resins than the industrial OEMs – take great comfort that resins like GreenPoxy 56 not only bring environmental advantages, but also make small workshops safer too.
How is the industry pushing your team to continue its developments for future products?
The key focus is performance. We must create products that allow customers to maximise their production efficiency and deliver the performance that their customers expect. In parallel, we continue to work on improving sustainability, improving the safety for people that use them and increasing the long term performance and durability.
The new SZ 8526 EVO hardener that we’ve developed is a perfect example. It cures for as long as the existing cure cycle and allows customers to reduce press temperatures. Not only does this lower their energy consumption and greenhouse gas contribution, but it is also safer for the production team as its CMR and SVHC free. This sort of development is something we’re proud of, working with OEMs to create cleaner, safer products that build better skis and snowboards.
www.sicomin